Online Fuel Inspection
A Proven Method
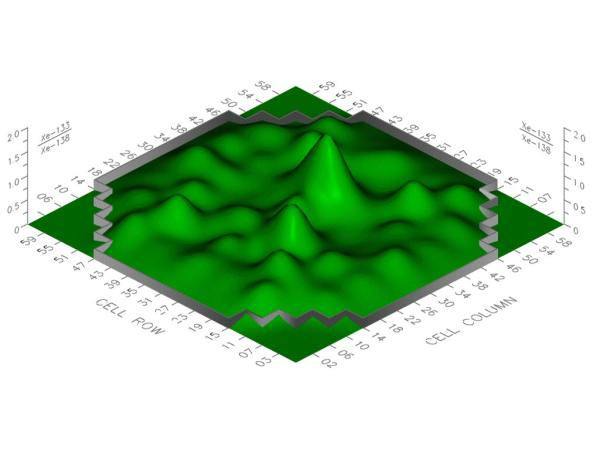
- A proven on-line method for identifying fuel failures in boiling water reactors
- Potential for avoiding costly ($3 to $8 million) plant shut down
- Offers off gas activity reduction through local power suppression
Unique Features
RSI's patented method for precise fuel rod leak detection has been established as "the state-of-the-art" methodology. It is a proven technology having been successfully used at many BWR's. The method is fast, reliable and can be applied with minimal impact on normal plant operations. RSI's team has the ability to quickly respond when the first sign of a potential leak is observed by a plant. The RSI method enables a plant to avoid a costly shutdown or long-term operation at reduced power levels.
Background
Failure of fuel cladding in a BWR has been an industry problem for many years. These failures have been primarily caused by one of three mechanisms: debris (fretting), manufacturing defect, or the interaction of the fuel pellet and the rod inner cladding surface.
Ameliorating the effects of fuel cladding failure by early detection has the potential for saving a utility millions of dollars during a fuel cycle. In addition, with early detection larger secondary ruptures of the cladding may be avoided. Fuel vendors have determined that the best way to prevent the onset of a secondary failure is early identification of the primary leak and power suppression for the associated cell containing the leaking fuel bundle.
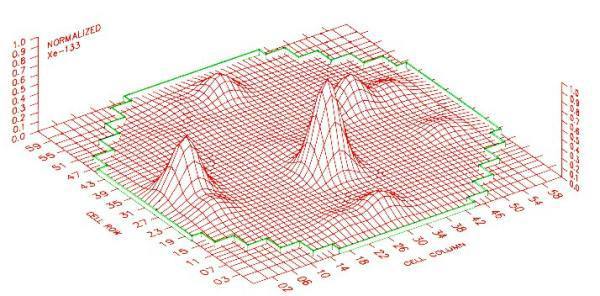
Traditionally, there have been two methods to detect leaks while the plant is still operating. The first method is to use the station offgas radiation monitors to observe changes while control rods are manipulated. This method is useful for large leak rates, but if the leak is very small, the change in offgas radiation levels may go undetected. In addition, the fuel vendors suggest reducing plant power to about 65% to prevent power spiking within a cell during rod manipulation testing. This power reduction further reduces the ability of the station radiation monitors to detect small leaks.
The second method involves obtaining samples of the offgas and analyzing them in the station laboratory. This method can be quite time consuming as the analyses must be delayed to allow the overwhelming radioactive nitrogen and oxygen components to decay. Furthermore, sample acquisition must be precisely timed to any control rod movement because only a relatively small sample of the total offgas flowing stream (15 cc) is sampled.
Description
RSI’s proven method for detecting leaking fuel rods involves manipulating the control rod in the area of the suspected leaking fuel rod. The variation in power in the associated fuel causes a change in the internal energy of the rod, forcing or allowing any gases inside the cladding to escape through the failure point. These gases are sampled and analyzed for specific indication of the leaking fuel.
A special chamber fitted with a shielded and collimated gamma spectroscopy detector is installed in the plant's offgas sample line. By detecting the various gamma ray energies, the precise composition of the offgas stream is determined. The observed changes in the composition and quantities of the fission gases during control rod manipulation in a fuel cell (four fuel assemblies plus one control rod) can be used to determine whether or not a leaking fuel assembly exists. For example, there are six gamma emitting fission gases of particular interest. Measuring the yield (relative amounts produced) and distribution of these gases, allows the magnitude and characteristics of a leak to be determined. This accurate methodology allows for quantitative measurement of all the gases in the offgas stream. Therefore, fast and reliable determination of the precise location of a leaking assembly can be made.
While the testing sequence is being performed, real time assessment of the analytical data is performed for immediate feedback to the plant. Thus, the sequencing can be optimized to isolate the leaking fuel assembly and return the plant to full power operation as rapidly as possible. Testing an entire core can be done for most plants in about 60 hours by structuring the test sequence to include multiple control rod movements.
Savings
By accurately identifying and suppressing a leaking assembly(s) using the proven RSI technology, a utility can avoid costly unplanned shutdowns, saving from $3 to $8 million dollars . On-line identification of the defective cells can also assist in limiting the scope of future fuel off-load and sipping operations. Moreover, successful suppression of failed fuel assemblies allows for continued operation at 100% power.